Which ERP to use?
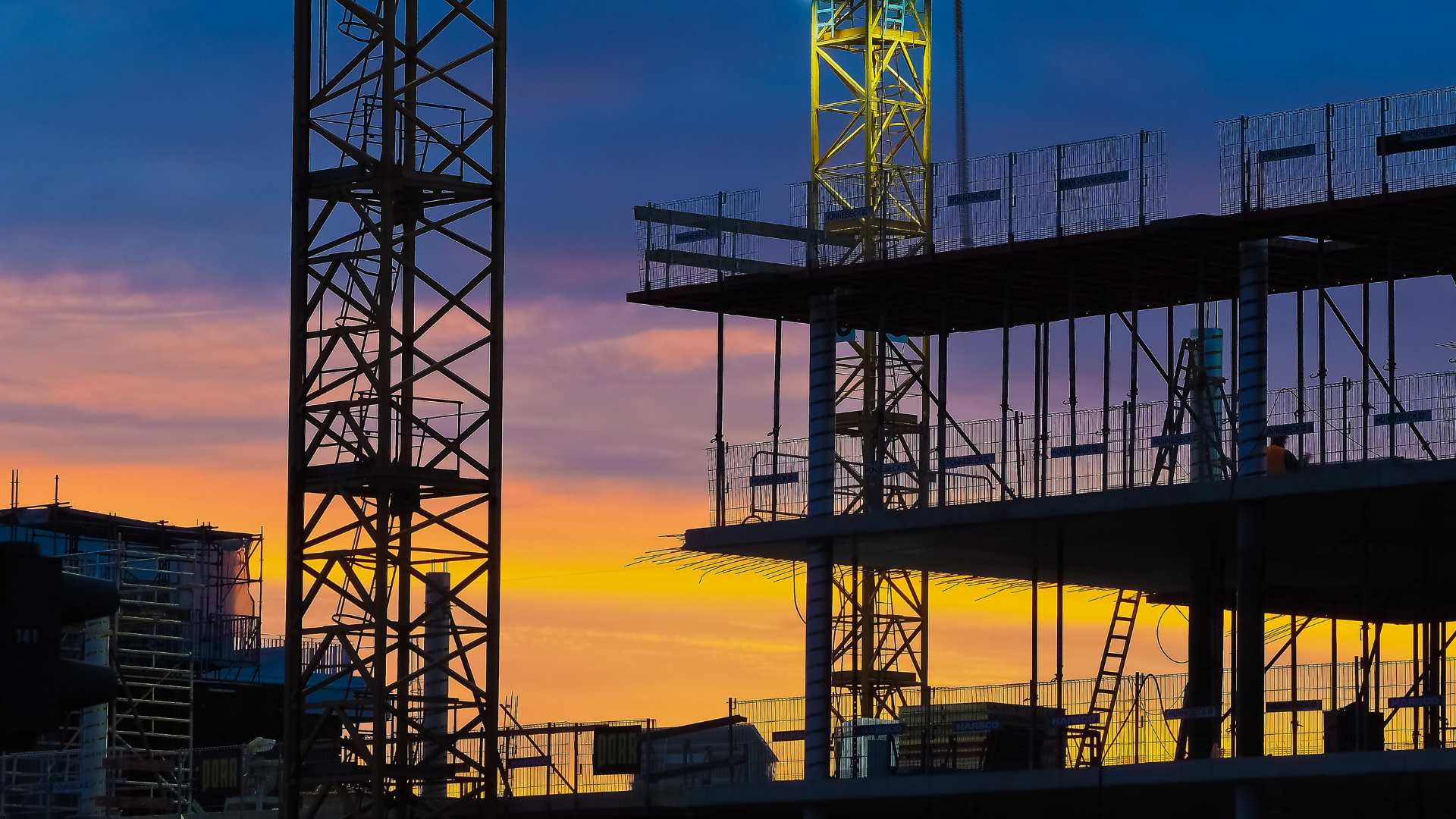
I have often been asked by consultants, contractors & property developers alike which ERP (short for Enterprise Resource Planning) software or tool to use to manage their business or control cost. Having gone through pros & cons of several options & studying the needs of end users, my answer is there is no one size fits all tool that addresses all challenges. In fact, many ERP systems today are so complex that they create more problems than solutions to the users if the top management is not 100% behind the initiative. Most companies look at an ERP as a solve-all kind of band-aid that will help them turn their companies into some sort of super performers overnight. The sad reality is the enormous challenge it poses to have a full-fledged implementation done & more importantly follow up religiously to improve & customise to suit specific needs of the industry / company.
Some of the features to look out for when going for an ERP implementation are: Interoperability – ability of the platform to function seamlessly across systems & devices, Customisation options & ease of adoption, Scalability, Availability of skilled manpower to manage & operate and sustained support of the service provider throughout the implementation life-cycle. Another important factor is the commitment of domain experts within the company to spend time, think through & assist the implementation team in coming up with an effective platform that is tailor-made for the company rather than be content at accepting what is given. What works for a contractor in the infrastructure segment will not work for a contractor in the buildings sector or come to think of it, may not work for same contractor operating in different sectors – like those operating in infra & building segments. The main point here is the identification of key drivers of the business – be it total volume of concrete to be pumped in or being cost conscious on a particular excavation item that has highest potential for margin or cost overrun and then drill down necessary checks & balances to ensure that these are monitored closely and controlled well in advance of the event happening so that desired results are achieved by design rather than by chance. It is this enhanced predictability that is often promised but seldom realised that is at the back of many failures of ERP implementation. What works for a company in another sector (say aviation or telecom) would not work for construction industry which has its own nuances & complications and hence before making decision on which ERP to use, it may be worthwhile to check any analogs or industry installations done by the implementer and check out the success factors.
Many a time, people tend to forget that the efficacy of any information management system lies in the quality & freshness of data. It is here that adequately trained personnel need to be deployed to ensure data capture is accurate & current so that the output of the ERP is useful & reliable. Most instances of cost & time overruns point to these shortcomings in spite of having a robust & best in class ERP system in place pointing to the fact that it is not the ERP per se that is the culprit but the other underlying factors that matter. Having been part of ERP implementation team of a very large conglomerate some 20 years ago and interacting with hundreds of companies since, I can easily conclude that it is not how fancy or robust the ERP is but success or failure of implementation depends on other factors that one need to be wary of & committed to see through while going for an ERP for the construction industry enterprise.
All said & done, it is not all dooms day but trying my bit to point to potential pitfalls so that your implementation is successful as after all, one needs to spend considerable resources in choosing & implementing an ERP system and a few words of caution would help.