Technology for Transformation of Construction Industry in India – Wishlist for 2024
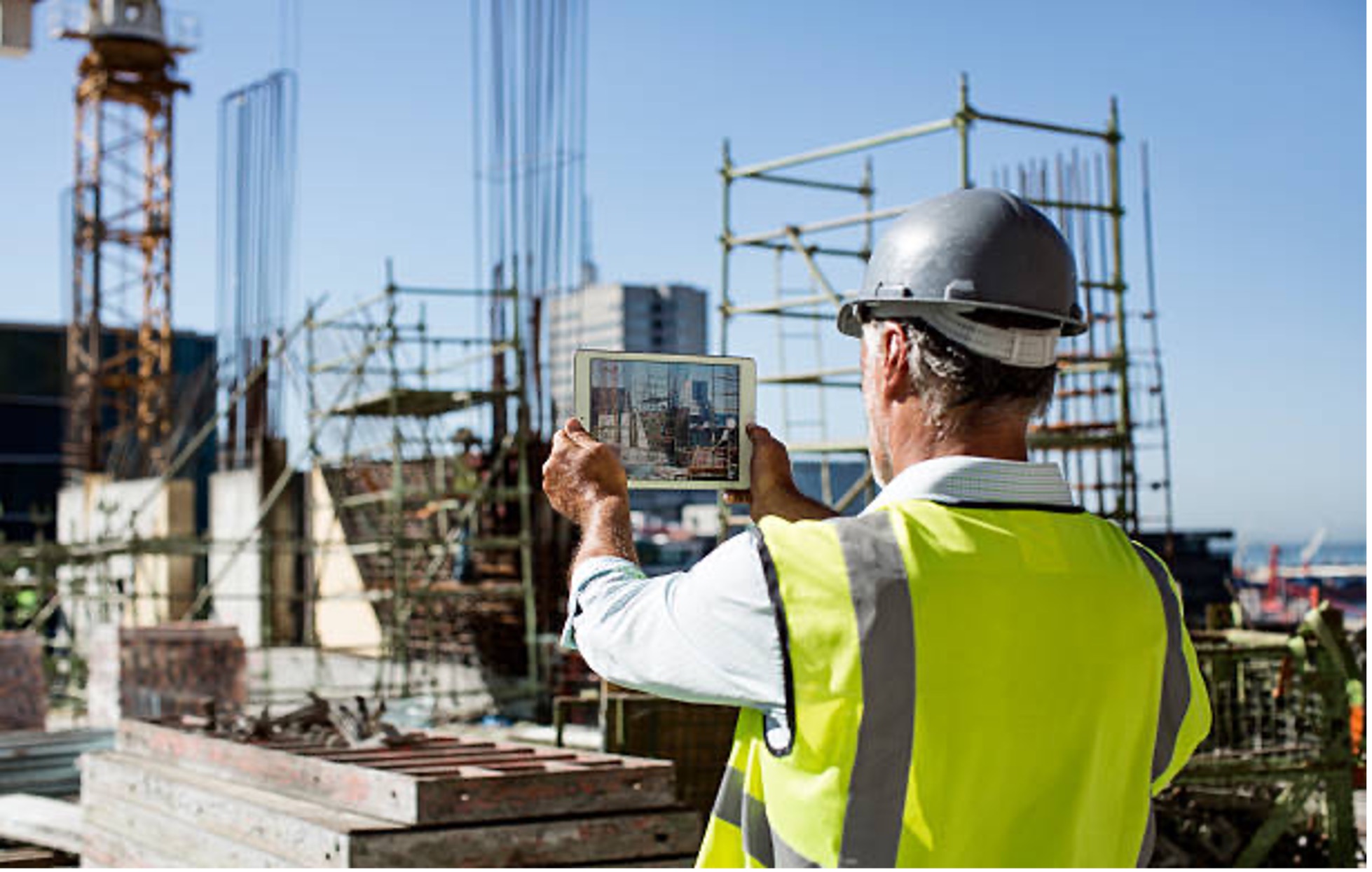
As curtains draw on another year and bring in new year 2024, I can’t help but ponder on some of the transformative changes that happened in the year that went by in construction industry in India and more importantly think of what is in store in 2024 & beyond. If we are to make the transition from being a laggard in adoption of Information Technology & Innovation to leadership in years to come, we need to take several quantum leaps in several areas that hold promise.
A cursory look at the developments from around the world tell us that steel & composite buildings and precast modular construction have grown by leaps & bounds establishing themselves as a go-to technology for anything done to scale or where replication is the key. There has also been considerable progress made in use of 3-D printing technologies – most notably in the USA, Europe and China. Whereas, we as a country, seem to have done reasonably well in adapting composite steel & precast modular construction technologies in buildings, we are yet to reach the full potential of the available cutting edge technology from around the world especially in highrises. Not to be outdone, we have also successfully ventured into construction of 3-D printed buildings opening up another frontier for the industry in India. These technologies are expected to continue the robust growth seen the recent past. If one were to see the past trends in these technologies in countries where it is in mature stage now, it is clear that from the early stages (similar to what we are today), there was a rapid industrywide adaptation leading to aggressive scaling up of the capacities by the stakeholders concerned. Not least of all is the vision with which the governments in these countries recognised the benefits of this shift from conventional methods of construction and encouraged industry through pro-active measures to adopt standards & work methodologies from design to handover thereby paving way for industry-wide technology proliferation & transition.
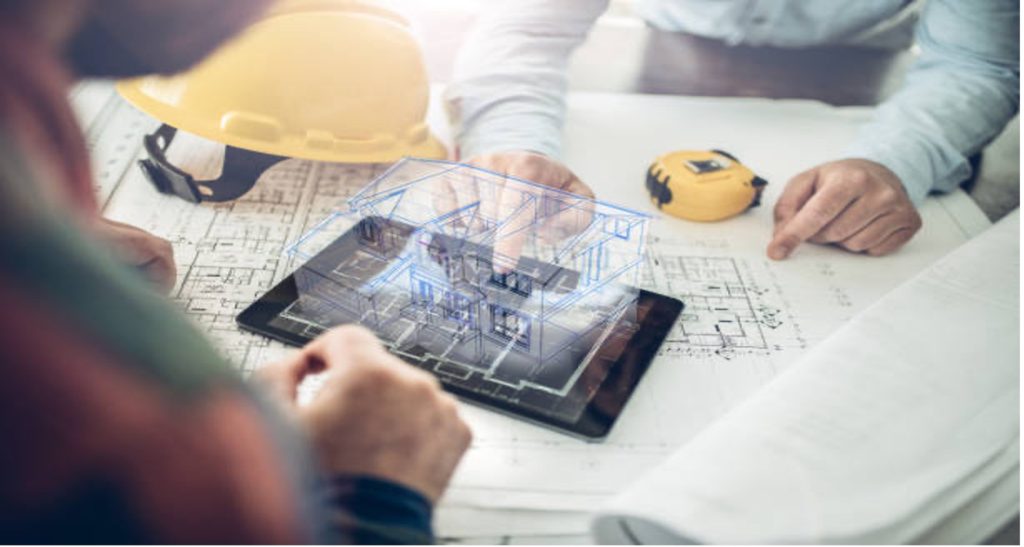
Now, coming to the subject of this Wishlist, whereas we seem to be making the usual lower double digit growth year on year in areas of composite steel & precast modular construction in buildings, the desired impact & benefits are far from reaching the entire industry & across the geography with vast sections of our country still far behind in reaping the benefits (which is one of the primary purpose of any disruptive technology, I suppose) due to several reasons. Firstly, these involve fusion of not just construction technology but also IT (both software & hardware), logistics, supply chain alignment and trained workforce. Secondly, the challenges of raising fresh investments into the sub-sector which by nature is capital intensive and carries its own fair share of risks which create entry barriers to newcomers. Having proven the benefits of these two developments whether it is in terms of economy of scale, reduction in timelines, optimization of scarce resources or elimination of in-built inefficiencies from the legacy system that is plaguing the construction industry for long, we seem to be not getting the required traction to move to mass adaptation across critical sectors like public housing, highrise construction, private residential & commercial developments in the built environment space.
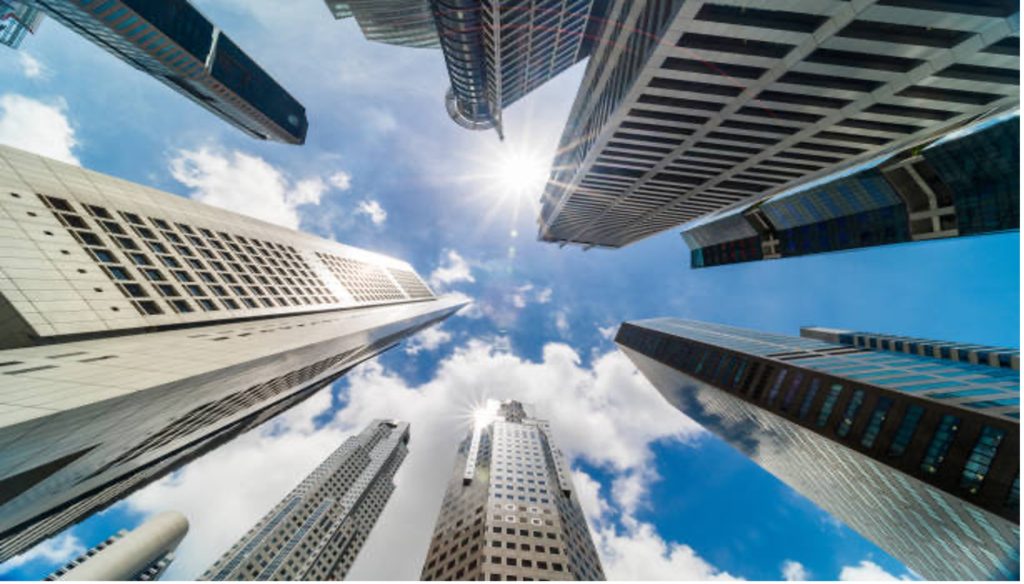
Taking an industrial approach to construction activities right from concept stage is one of the primary reasons for lacking mass adaptation – whether it is sensitizing the designers to focus on manufacturability of their ideas or giving heads-up to producers who have to grapple with synchronizing the design possibilities with the production of suitable grades & sizes as well as its easy availability could be one of the ways to overcome the resistance of stakeholders to switchover to composite steel or precast modular construction in buildings. Easier said than done, this calls for intense intra-industry brainstorming & standardization with some industry body (be it government or non-government) taking a leadership role. I do agree, there are also other challenges like severe shortage of skilled professionals – be it the designer / detailer, welder/fitter/rigger or mould designer / foundry houses, availability of expertise in software & hardware like BIM, CAD,CAM etc, developing required techno-legal and techno-commercial frameworks to address contracts or logistics backbone that is at the core of composite and modular construction. These, I believe, could be addressed along the way once there is alignment on opportunity. Besides, if one were to go by the total volume of works done in these technologies compared to all the building works done, it appears the market size also has not attained critical mass to give a truly market driven competition to existing players which is also hindering innovation, competitiveness & development within the industry.
The non-governmental organisations in the sector, on their part, could do much by formulating implementation roadmap and policies recommending minimum usage of structural steel / composite and precast modular construction elements starting from say 10 to 15% (of either the cost of construction or number of elements) and gradually set a roadmap for industry-wide improvement over the next 5 years or so to reach full adaptation. This will give time for the industry to bring in fresh investments, develop standards, technology transfer, training & skill enhancement and infrastructure ramp up. This has been done successfully on a large scale in countries like Japan, South Korea and Singapore to name a few where the entire industry made the transition over a period of time from more or less similar situation as that of India today. This transformation from a conventional, inefficient, manpower intensive, low-quality industry to one of highly efficient, skilled and high quality, high value-add industry would not happen automatically or just like that but by sustained efforts of multiple industries and government agencies committed to make it happen. To imagine that this transformation happened in these countries in less than a decade and now with available lessons learned and access to IT, the transformation in India can happen in a much lesser period (as we need not go through the first comer pains & learning by own mistakes) if government and the industry at large decide to sit together to plan & effectively implement a well laid out strategy is what interests me the most. Nothing short of this would work in a country as vast & diverse as ours where economics, practices, mindset etc., all change dramatically every 150 kms or so whichever direction one goes. Without this rapid implementation with government support and complete industry involvement, it would be difficult if not impossible to achieve the dream of housing for all and building a sustainable & highly efficient industry on par with world leaders. Left without action, the gap can only widen between us and other adapters thereby depriving our industry of exploring options of business opportunities in these areas in other countries where there is potential.
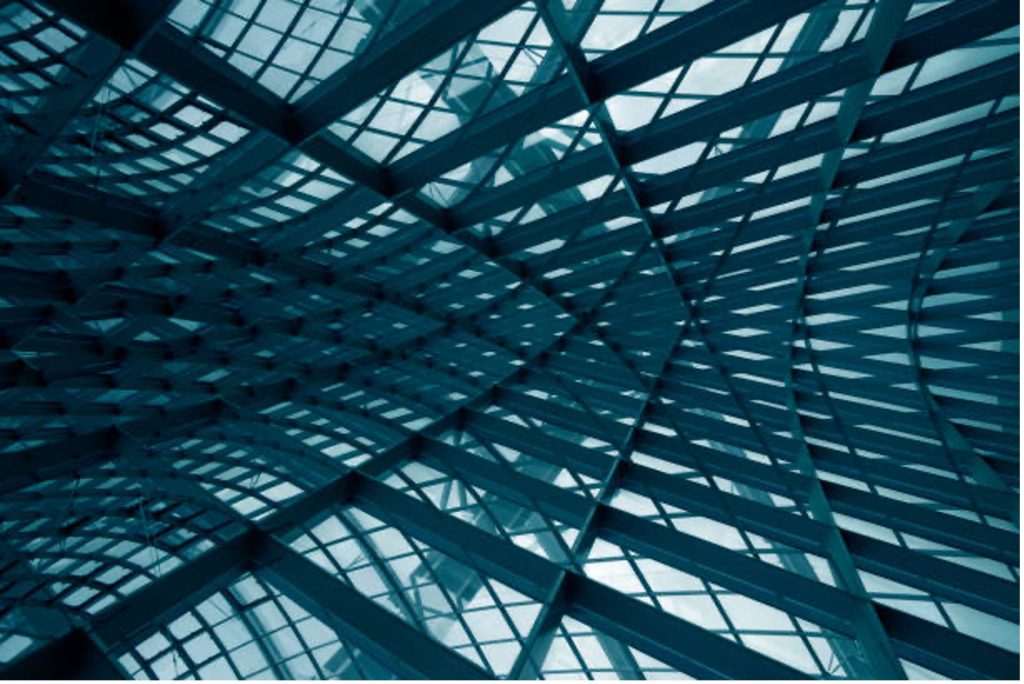
It is not that the government cannot intervene, formulate & effectively implement forward looking policies – it has already done so with remarkable success in other areas like IT/ITES, Biotechnology, Automobile, Manufacturing, Telecom, Defence and most recently in Space sectors where the respective industries / sectors have harmoniously & in full vigor supported & benefited from these initiatives. Hopefully, all the stakeholders will prioritise construction industry as a fit case for transformation in the current year so that the industry can reach its true potential & contribute even more to nation building.
I agree that this may not be the panacea for all the challenges faced by construction industry, but seems like it has the potential to lift the entire industry in a higher orbit.
Here is wishing you a successful year ahead!